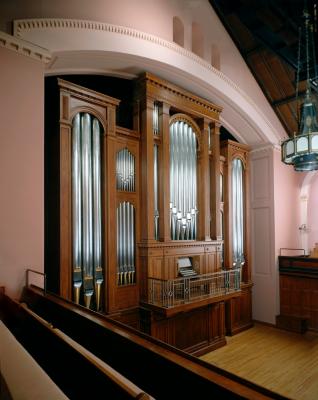
Keep your distance.
In both the May and June issues of The Diapason, I wrote about watching the world react to the spread of the novel coronavirus. I have told you how my family and I left New York City for our place in Maine, leaving behind the horror of the spread of vicious contagion in a densely populated city. Individual boroughs of the city have higher death tolls than many countries, and our friends there tell of fear and loss. As I write in mid-May, there have been over 160,000 cases confirmed and over 13,500 deaths in New York City. There have been thirteen cases and no deaths confirmed in Lincoln County, Maine, where we live.
We left New York two days after Broadway, Lincoln Center, and all the museums of the city were closed, that great engine of culture, those vibrant theaters, those stately crowded buildings all going dark at once. By that time, virtually every college and university had closed or was closing. Social media pages became clamors of teachers comparing notes about how to teach from a distance and students facing unprecedented interruptions in their education. I am particularly well connected on Facebook where my community includes some three thousand organ professionals, and I have been impressed by the thoughtful interchange.
I wrote a post asking colleagues if they would be interested in talking about distance learning and, with a half dozen responses, spent more than ten hours last week on FaceTime, Zoom, and video chat (and on the phone when the internet got slow), conversing with friends and colleagues about how they were developing methods to cope with this untenable situation, keeping the wheels of learning turning.
Necessity is the mother of invention.
The common opener was that it is nobody’s first choice to close a campus and send students home, there is no precedent, and we had better figure this out. The biggest variable is whether students have access to organs, pianos, or even cheap keyboards during the closures. When away from campus, students live in a wide variety of circumstances. While some students go home to luxury, others return to poverty where shortage of food is an issue, never mind whether there is a piano, let alone an organ. Before being able to establish connections to continue teaching, some teachers have petitioned their schools to provide instruments, WiFi connections, and, in some cases, food.
Christa Rakich teaches organ performance at Oberlin Conservatory of Music, where students were informed a week before spring break that the school was closing and they needed to vacate their dorm rooms. There was a flurry of activity as clothes, books, and personal items were packed and parents came to help ferry stuff home. There must have been a shortage of cardboard boxes in town.
Because Zoom and other video conferencing platforms can be shaky and imprecise, Christa is using video recordings as a primary tool for private lessons. Students send recordings to her that she watches with scores and sends emails with comments referring to measure numbers. “It’s tedious progress, but it’s progress, and helpful for them to have my return email in hand for the next practice session.”
Christa is also sending weekly “Improv Challenges” to her students by email. In an email before our conversation she wrote, “I submit this with an audio file. I record myself improvising, for example, a two-voice chorale prelude or a pedal cadenza or a fugal exposition in three voices with a cadence, something contained and short. The email includes instructions on how I did it or perhaps a written sample. Students are challenged to send me back an audio file using the same technique with a different tune.”
Early on, Christa experimented with live playing over Zoom for studio class, but found that the platform was unstable, so she and her students have spent productive time together planning future projects, working hard to keep a productive learning environment in place as much as possible. According to Christa, the administration of the school is encouraging students’ ideas for study projects and reading, supporting their creativity by giving credit—“everything you do counts as work.”
Andrew Scanlon is assistant professor of sacred music and organ performance at East Carolina University and organist at Saint Paul’s Episcopal Church in Greenville, North Carolina, where Andrew’s students are accustomed to having their lessons on the spectacular forty-five-stop C. B. Fisk, Inc., organ (Opus 126, 2005). The university has supplied the faculty with tutorial videos on distance learning helping Andrew to develop techniques for video teaching, and he has been able to find access to organs for all his students. He reports that the organ literature course he teaches has been easiest to transfer, mostly by giving lectures online. He is guiding students toward the AAGO exam and continuing their improvisation training.
Nicole Keller has been teaching organ and harpsichord students at Baldwin-Wallace Conservatory of Music, Berea, Ohio, for twenty years. During our conversation, she spoke of how the school’s administration has been sharing information openly with bi-weekly video town hall meetings for the faculty, and the school’s IT department is helping with information about available resources and helping to get students online. Nicole is facing this disruption, wondering how she can use the experience to become a better teacher. She is finding the exchange of recordings to be effective, and to a lesser extent, playing through Zoom. She added that external microphones for laptops make a big difference in the sound quality, especially when using Zoom, and mentioned that the conservatory has provided microphones for the students.
George Emblom teaches at the University of California at Berkeley and is director of music at Saint Mark’s Episcopal Church in Berkeley. He started our conversation with the simple comment that this is unprecedented. No one expected this, and no one had planned for it. With the campus and church building closed, he has been able to secure access to instruments for his students, even in some cases through loans from members of the choir at Saint Mark’s where his students have their lessons on the Flentrop organ.
We are all learning and developing the art of distance teaching simultaneously, and George believes that some of the new techniques will continue to be useful when we are able to return to teaching private students face-to-face. He particularly mentioned shared video recordings, commenting that he is spending a lot of time watching the pinwheel on his screen as videos are downloading. Students send videos to him through Google Drive, and he shares his screen with them, allowing student and teacher to watch together in real time. He has found that students benefit greatly from watching their performances, seeing their posture, hands and feet, and the motions of their bodies, both useful and unnecessary. “At measure 43, do you think you looked comfortable?” He intends to continue using this tool in the future.
George’s performance degrees are in piano. Remembering that there were always two pianos in a teacher’s studio so the teacher could demonstrate, he has been using the piano more extensively as a teaching tool and considers this another technique to be developed and used more in the future. He also reminded me that the concept of distance teaching for serious musicians is in its infancy. He is in conversation with colleagues around the country comparing and assessing techniques and imagines that new and more powerful platforms will be developed quickly.
Jonathan Moyer is assistant professor of organ and chair of the organ department at Oberlin and organist at the Church of the Covenant in Cleveland, Ohio. He is teaching some private lessons with students sending him recordings followed by video conferences, usually on Zoom. But he is really focused on finding new ways for students to learn. Organ literature classes are productive as he can provide listening lists on YouTube. Students “mute out” to listen, then return for discussion. He shares PowerPoint slides on Zoom and gives out reading assignments, some of which temporarily take the place of performance.
Oberlin is well known for its extraordinary collection of more thirty organs, and Jonathan feels that a big part of education there is being on campus with those instruments, sharing musical inspiration in person with students and teachers. He feels that most of his students have had enough of the “video thing.”
Katherine Johnson is a third-year student of Christa Rakich at Oberlin. She spoke of the shock of being told to vacate her dormitory just before spring break. She is working hard to make the most of it and is fortunate to have a Hauptwerk instrument in a relatively private space at home where she is working on the “self-taught” piece she has chosen for her jury, whenever that will be. In course work, she notes that her fellow students are in different time zones, which makes it difficult to schedule class meetings online, but she is generally impressed by how video platforms make distance learning possible.
§
I am grateful to the six people who spoke with me last week. Each spent an hour or more with me and shared not only how they are approaching the different acts of teaching and learning, but also about their concerns for each other. All five of the teachers echoed their concern for the well-being of their students, many of whom have been shuttled off campus into stressful situations of crowded houses full of distance learners and parents working from home. WiFi is everything, and housemates are having to negotiate for bandwidth. Students who are strongly self-motivated are finding rich new ways to learn, while others are struggling with the difficulties and uncertainties of their situations and the disruption of their education.
As of this writing, none of the schools involved has yet made announcements regarding the status of the fall semester. Jonathan Moyer mentioned that Oberlin would be deciding by mid-June whether to open the campus for the fall, perhaps without large ensembles and with limited class sizes. Different schools are considering having only single rooms in dormitories and somehow staggering the semesters, a scheme that falls apart in a hurry when you get to communal bathrooms.
All of the teachers spoke of the spirit of camaraderie and cooperation among students. Everyone I spoke with mentioned fatigue, especially screen fatigue. Even if you are used to spending hours in a practice room or teaching studio each day, you are still moving around between classrooms, offices, and dormitories. Likewise, there was a lot of talk about maintaining energy, keeping things lively and inspiring in online discussions. Teachers are spending lots of time just talking with their students, helping them redefine their dreams and ambitions while staying optimistic.
And what about church?
All but one of the teachers I spoke with also serve as church musicians, and each shared a little about how online worship is working. Very few church buildings are open, so most are either sorting and streaming recordings from years past, or recording preludes, postludes, and hymns on whatever instrument they have at home.
Last month we published a photo of John Cantrell, choirmaster and organist at Saint Michael’s Episcopal Church in Manhattan seated at the desk he has adapted for the production of the church’s video services. He described to me the challenge of creating an essence of worship for the congregation. He has always been interested in audio engineering, but “this video thing” is new, and he has been learning on the job. He and the clergy have been drawing on the example of Mr. Rogers and his legendary ability to communicate on television with children. How did Mr. Rogers draw children into the screen, suspending their disbelief, and can we emulate that in online worship?
At Saint Michael’s, the organ scholar records a prelude and postlude in the empty church with John as the videographer, allowing the congregants a rare glimpse of the organist who is normally hidden by the Rückpositiv of the great Beckerath organ. They also record at least two hymns, generally one verse for each, and show the text on the screen so “distance congregants” can sing along. John records a rehearsal track for an anthem that he sends to choir members who practice and record their part, and they send it back to John who stacks the tracks, tweaking the early or late notes as needed, and mixes the whole thing into a choir. This is far from perfect, and many people are unable to participate, especially elderly parishioners with no internet skills. We can suppose that powerful apps will be developed making all this possible without the need for each music director to reinvent the wheel.
A common concern is the future of choirs. On April 29, The Guardian reported that the German government had met with church leaders and agreed that when German churches open for worship in May, singing would be prohibited. The article noted that three quarters of the members of a church choir in Mount Vernon, Washington, fell ill and two died, and that fifty-nine of seventy-eight singers in the choir of Berlin’s Protestant cathedral contracted the virus. On March 8, the Amsterdam Gemengd Koor (mixed choir) gave a performance of J. S. Bach’s Saint John Passion in the Concertgebouw, the city’s famed concert hall. Of 130 singers, 102 contracted COVID-19 and four died. The American Choral Directors Association has issued an announcement to its membership stating that singers are “super spreaders” of the coronavirus because singers breathe more deeply than normal and expel breath at great velocity. A group of people singing may as well be sneezing on each other.
Andrew Scanlon said the reason the choir at Saint Paul’s in Greenville sings psalms so beautifully is that they do it all the time. It is in their blood. Will choirs have to wait years before being able to gather again? How much interest, proficiency, and experience will be lost?
Lemonade
We have no idea how long this will last. My family and I came to Maine thinking we would be here for a few weeks and have now been holding in place for over eight weeks. Given our usual lifestyle with two homes and a significant amount of business travel, this is the most consecutive nights I have spent in one place in nearly twenty years. The statistics of the epidemic as some states try opening selected businesses may indicate that we will be in this longer than we have yet imagined. From our seclusion, it is impossible to imagine when we might next enter a Broadway theater with twenty-inch wide seats and endless lines for the restrooms.
Most organists are employed by churches or universities. Although playing the organ seriously is a solitary venture, both types of institutions depend on people working in groups. Seminars, classrooms, staff meetings, faculty meetings, and especially choirs are important to the work of the organist. At the moment, the challenge of setting up distance learning and distance choral singing is taking more time for many people than the familiar weekday rehearsals and Sunday services.
Once you have mastered and improved the techniques, will you have more time for personal projects? Is this your chance finally to learn those last eighteen pieces so you can say you have played all of Bach’s organ music? The Vierne symphonies? How about some of those pesky masterworks by Rachel Laurin or Jeanne Demessieux? Maybe it is time to finish and submit that article to The Diapason? Spend some more time with Beethoven’s piano music? Or admit it, you have always wanted to take the FAGO exam. Contact your chapter leadership and sign up. Maybe you were going to spend a week or two at conventions this summer. How often have you wished for a couple extra weeks to tackle something you have always wondered about? Guess what, kids, now’s the time.
When we meet on the other side, let me know how you did.
C. B. Fisk, Inc., Opus 116, Finney Chapel, Oberlin College, Oberlin, Ohio (photo courtesy: C. B. Fisk, Inc.)